Turnkey 5-7T/H Chicken and Cattle Feed Mill Plant for Ethiopia Customer
Recently, we successfully delivered a complete 5-7T/H feed production line to a client in Ethiopia and a comprehensive turnkey solution. This project showcases our integrated capabilities in feed production line design, equipment manufacturing, installation, commissioning, and customer support. Below is a detailed project overview, including background, solution, implementation process, and customer feedback.
Project Background: Customer Needs and Selection Process
The client found us through an online search and, after comparing multiple suppliers, ultimately chose us as their partner. The client had clear and specific requirements:
Automated Production Line: The client required a highly automated production line to reduce manual intervention and ensure precision and efficiency in feed production.
Flexibility: The production line needed to produce different types of feed, especially poultry and cattle feed. It required the ability to produce both pellet and powder feed and pellets of different sizes.
Space and Equipment Configuration: The client wanted the production line to efficiently use factory space and required storage facilities for raw materials and finished products.
Turnkey Service: The client requested a one-stop turnkey solution that covered everything from design to installation, commissioning, and training, ensuring smooth operation from factory construction to production startup.
After thoroughly understanding the client's needs and local market conditions, we provided a comprehensive feed production solution that included advanced production equipment, complete factory design, construction, equipment installation, system commissioning, and operator training.
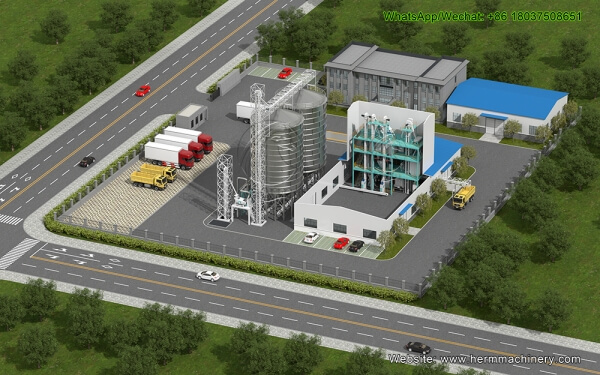
Solution: 5-7T/H Feed Production Line
We designed and delivered a 5-7T/H feed production line for the client, equipped with a full set of equipment covering raw material storage, batching, production, cooling, screening, and packaging, ensuring both efficiency and flexibility in production. Every aspect of the design focused on optimizing production processes, reducing energy consumption, and improving product quality.
1. Production Line Configuration and Process Design
Production Process: Based on the client's needs, the entire production line covers multiple stages from raw material processing to finished product packaging.
Raw Material Grinding System: We provided high-efficiency grinding equipment capable of adjusting the grinding degree based on the type of raw material, ensuring the ground materials meet the requirements for subsequent processing.
Mixing System: The mixing system utilizes an advanced fully automated mixer that ensures precise mixing of different raw materials, ensuring uniformity and nutritional balance in each batch of feed.
Oil and Molasses Addition: For the client's specific formulation requirements, we designed a dedicated oil and molasses addition module. This system precisely controls the amount of oil and molasses added during the mixing process, ensuring stable feed quality.
Pelleting and Cooling: Our pelleting system can produce pellets of various sizes, efficiently and stably pressing the mixed raw materials into pellets. To prevent overheating of the pellets, we included a cooling system to ensure the pellets' hardness and appearance are maintained.
Screening and Packaging System: To ensure the quality and appearance of the final products, we designed a screening system at the end of the production line to remove substandard pellets. We also provided an automated packaging system, which can pack products in bags or load them in bulk, depending on the client's needs.
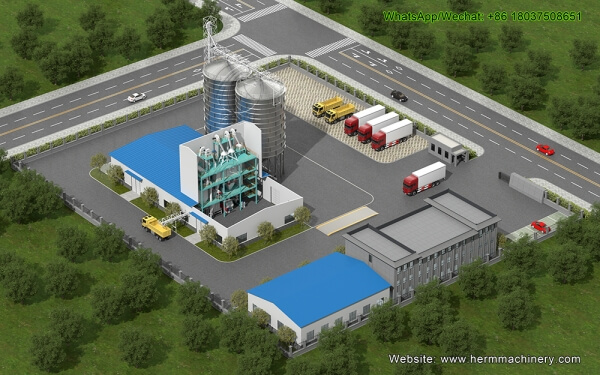
2. Automation and Smart Control
To increase automation and reduce manual intervention, ensuring precision in production, we equipped the client with an advanced automatic batching system and PLC control system.
Automatic Batching System: The system automatically and precisely batches raw materials based on preset formulas, ensuring each batch of feed meets nutritional standards and consistency. This technology significantly improves production efficiency and reduces human errors.
PLC Control System: The entire production process is managed by a PLC control system. The client can monitor the operational status of the equipment in real-time through a central control panel, adjust production parameters, and optimize the production process. The control system enables full automation from batching to packaging, greatly improving production efficiency.
3. Dual Production Capacity: Pellet and Powder Feed
One of the key highlights of this production line is its flexibility. We provided the client with the ability to produce both pellet and powder feed, enabling them to switch production modes based on market demand:
Pellet Feed: When producing pellet feed, the client can adjust the pellet size and hardness by changing the pelletizing die and formula. This allows the production line to create various animal feed pellets, such as poultry feed pellets and cattle feed pellets.
Powder Feed: The client can easily switch to producing powder feed, adapting to the needs of different animals and market requirements.
This design greatly enhances the adaptability of the production line, enabling the client to respond flexibly to different product demands and improve resource utilization.
4. Large-Scale Storage and Bulk Loading Design
To improve overall production efficiency, we equipped the client with two 1200-ton steel silos, which provide secure storage for large quantities of raw materials and finished products. These silos have excellent moisture-proof and corrosion-resistant properties, ensuring long-term storage quality.
To address local transportation needs, we also designed a bulk loading system for the finished products. The feed can be directly loaded into bulk trucks, improving transportation efficiency and reducing packaging and labor costs. This design plays a crucial role in the client's feed distribution and transportation processes locally.
Turnkey Solution: Hassle-Free Service
We provided the client with a complete turnkey solution, covering every stage from initial design to final commissioning, ensuring timely delivery of the project that met all the client's requirements.
1. Factory Layout Design and 3D Visualization
At the start of the project, our engineering team tailored a detailed factory layout plan based on the client's site conditions and production needs. To help the client better understand the design, we used advanced 3D design software to create visualizations of the factory and equipment layout. The client was able to see a virtual representation of the completed factory in advance, ensuring that every aspect of the design met their needs and making it easier to make adjustments if necessary.
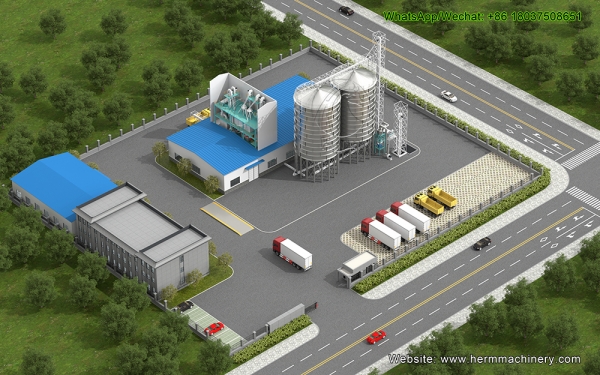
2. Installation and Commissioning
After the equipment was manufactured and shipped to the client's site, our professional installation team was dispatched to Ethiopia for on-site equipment installation. During installation, we strictly followed the design plans and quality standards to ensure the equipment was properly installed and that all systems complied with safety regulations. After installation, we carried out system commissioning to ensure that every part of the production line operated smoothly and produced feed that met the required standards.
3. Operator Training and After-Sales Support
To ensure that the client could fully utilize the new feed production line, we provided comprehensive operator training. The training covered daily operations, maintenance, troubleshooting, and other aspects, helping the client’s operators improve their skills and ensure the long-term stability of the production line.
After project completion, we also offered comprehensive after-sales services, including regular maintenance and technical support. The client can contact us anytime for technical consultations and emergency troubleshooting, ensuring the production line continues to operate efficiently.
Customer Feedback and Project Outcome
After the successful project delivery, the client highly praised our design capabilities, equipment quality, and overall service. They indicated that the high level of automation significantly improved production efficiency. The ability to produce both pellet and powder feed allowed them to adjust production plans flexibly to meet varying market demands.
The client was particularly satisfied with our turnkey service, which not only ensured on-time project delivery but also simplified their management processes, allowing them to focus on feed production and market expansion.
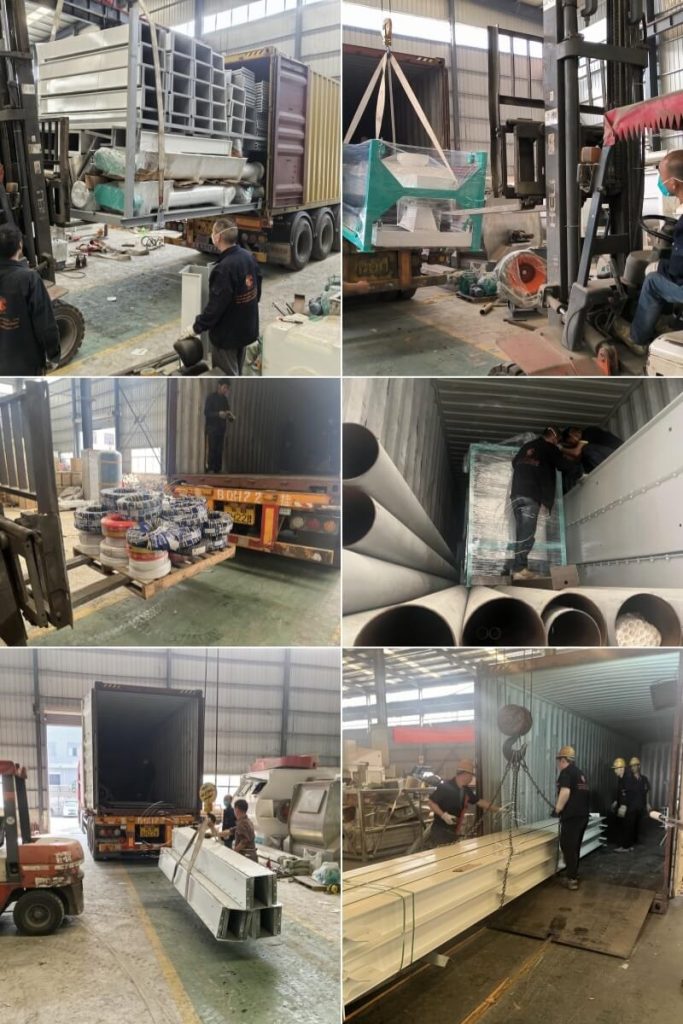
Conclusion: A Successful Example of Turnkey Solutions
Through this project, we once again demonstrated our expertise in feed production lines. From design and production to installation, commissioning, and after-sales service, we always adhere to a customer-centered approach, offering the most suitable solutions for each client’s needs. Our turnkey solution not only improved the client’s production efficiency but also enhanced their competitiveness in the market.
If you have similar production line needs, feel free to contact us. We will provide a customized solution based on your specific requirements to help you achieve your production goals.
Henan Herm Machinery Co., Ltd was established in 2010 and has been devoted to the research and development of Feed Mill Machinery ever since. With more than 10 years of experience, Herm® has become a leading manufacturer and supplier of animal feed machines and complete animal feed production lines, cattle feed plants, poultry feed plants, animal feed pellet production lines, etc. It always endeavored to improve the quality of products and aims to meet the new requirements of the international market.
If You Are Ready to Start a Feed Pellet Plant Business, please contact us for the feed mill machine. We Can Provide Professional Design and Comprehensive Guidance According to Your Needs. Get in touch with us now!
Welcome Contact Us!
Henan Herm Machinery Co., Ltd
Email: info@hermmachinery.com
Phone/Whatsapp: 0086-18037508651